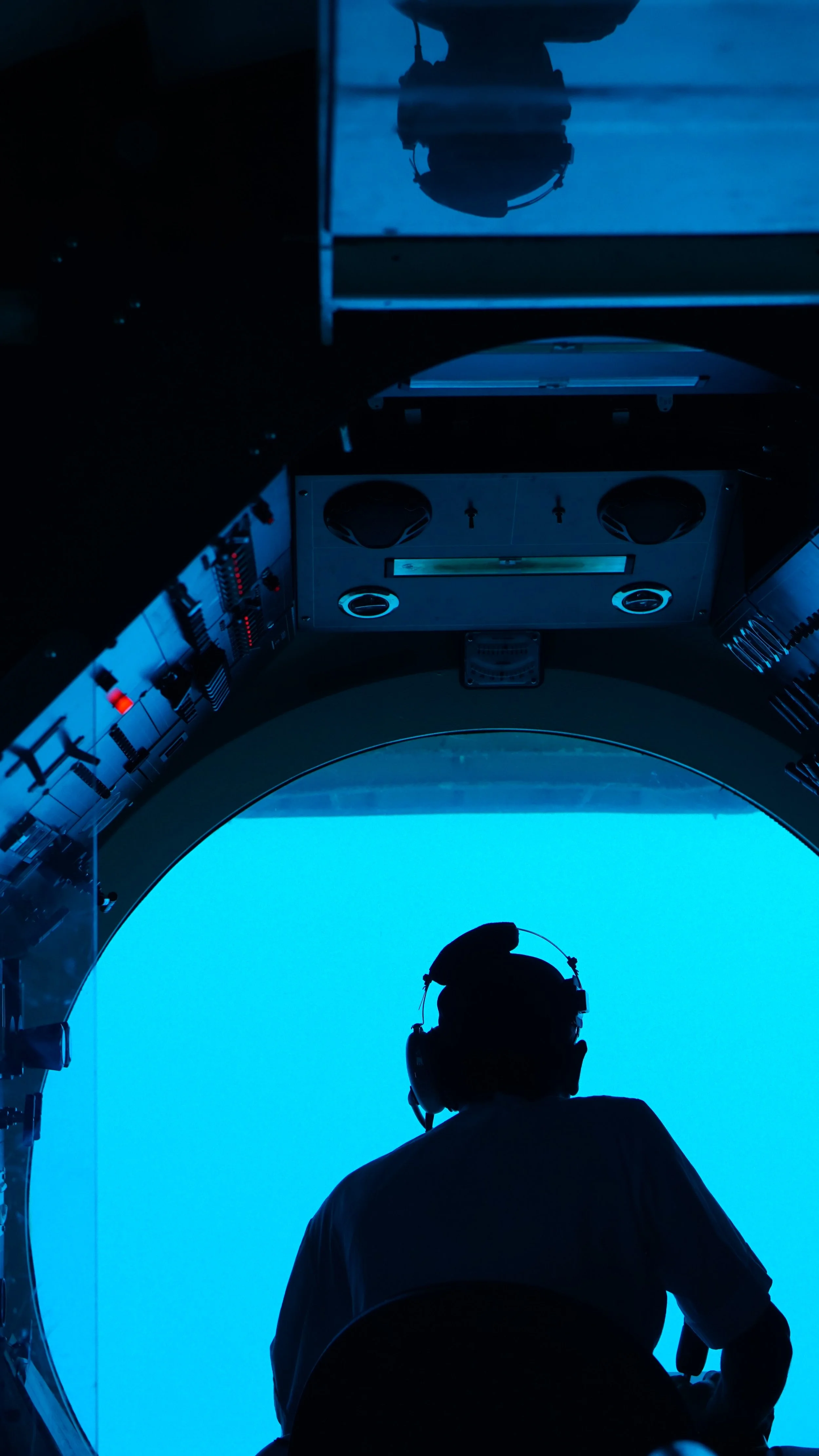
Are superoxalloy abrasives really that good?
At 10X Engineered Materials, our products are so different and our claims so bold that it is commonplace for our prospects to be skeptical.
We’re going to share a story with you…
About a gentleman who served in the U.S. NAVY on a submarine and then spent the remainder of his career maintaining submarines. He has always served his country with pride and he is passionate about his craft.
Dino first learned of 10X superoxalloy abrasives at a tradeshow. When one of his colleagues told him about the bold claims a new abrasive manufacturer was making, he had one thing on his mind… doubt.
After Dino met with our factory representatives, he decided to challenge our products in a real-world field test at the Portsmouth Naval Shipyard in Kittery, Maine. He was face to face with a mockup having over 100 mils of well adhered, marine coatings on a hot summer day. The blaster reported, “This stuff flies! It goes right through the coating… Congratulations on an impressive abrasive product.” Now, Dino’s doubt was fading, and new questions arose. How much faster can we go? Will a superoxalloy really delay rust bloom for weeks inside of an unconditioned tank? Will this deliver real schedule and cost savings?
Dino needed to see more and use the products in a real submarine.
He needed to involve the right people and try to solve the real challenges. He needed to see what results could be achieved at scale. Moving from a mockup to blasting the inside of an active nuclear submarine with a totally different, completely new and unapproved abrasive product involved taking a calculated risk. Nothing ventured, nothing gained.
Dino had the fortitude to ask his colleagues and their superiors to take this risk. They, too, were skeptical. However, the testing plan was submitted for approval.

“This stuff flies! It goes right through the coating… Congratulations on an impressive abrasive product.”
— NAVY Blaster
The Plan
Persist
A year later, Dino’s plan was approved. The USS Texas (SSN 775) was selected. With a testing plan approved, he moved forward. Work started in one of the sanitary tanks. The first observation was lower dust. The blaster could see his work area and he didn’t have to stop to vacuum nearly as often. The second observation was significantly lower consumption. The mechanics ordinarily refill the blast pots twice per shift but discovered that refills were only needed every other day.
Later in the summer, the work moved into the vertical launch system (VLS). New efficiency and schedule-compression records were set. Additional minds were changed at the shipyard. The workers, mechanics and inspectors all wanted to keep blasting with superoxalloy.
The Results
Excellence
Dino’s plan worked. The performance of the products surpassed the manufacturer’s bold claims. The entire team at PNSY was impressed and excited. What was achieved was not only unexpected, but unprecedented at PNSY. In just four small areas the abrasive saved 488 hours of labor.
The VLS was completed 79% faster and achieved an SSPC SP-5 white metal finish - the highest quality surface ever achieved in this application at PNSY. The sanitary tanks were completed 73% faster. This really is a better product and a better process.
-
Day 3
After blasting sanitary tank 1 - graded SSPC SP-5 white metal finish
-
Day 14
Graded SSPC SP-10 near white metal finish
What’s next?
Implementation
Stay tuned. The U.S. NAVY is leaping ahead of its adversaries: delivering higher quality in a fraction of the time with massive cost savings, all while using and discarding less material. Bravo Zulu, Dino!
-
Visit 10X at IWBS
10X Engineered Materials is happy to have a team of certified engineers attending the annual International Workboat Show. Visit 10X at booth number 958.
-
Book an Appointment
Unable to visit us at IWBS? Set up a virtual meeting to talk to one of 10X’s certified engineers to learn how superoxalloy abrasives can improve your process.